Sugar factory automation strategy
The solution is designed to be operated as a stand alone or as a second step of an integral part of a factory wide automation concept. In the next higher level of automation, the system is linked together with other areas of the sugar plant, central operation of the entire plant from a central control room becomes possible.
Contents
Introduction
Selection of automation strategy
Automation for the milling plant section
Automation concept for vacuum pan or sugar boiling process
General aspects of crystallization
Technological steps
Summary and conclusions
Introduction
The increasing pressure on sugar manufacturing companies to be more efficient in producing sugar is always the topic whenever sugar producers meet all over the world. The calls for greater plant efficiency, flexibility, environmental protection are common sugar industry requirement that should be the bottom line. These requirements implies that everything must work together effectively: process controls systems, automation and communication, electrical and drive technology as well as information technology. Solution is, once the sugar production is fully integrated, everything works better, likewise, a well-defined automation strategy is very vital in achieving the automation of the sugar factory.
Selection of automation strategy
The automation systems can be divided into two main groups:
- Centralized Control System (CCS). A system based on a powerful computer that controls and collects data for the entire factory floor.
- Distributed Control System (DCS). The factory is divided into small process sections each with a PLC or process computer attached.
To migrate from manual control with local control panel to a fully automatic CCS would be a very ambitious and cost-consuming project, if one will look into a quick return on investment. DCS is recommended to be used, which gradually extend process section by process section. This result in a simpler and reliable system, where different input and output modules can function as a stand alone units – independent of the operating conditions of the other.
In the concept of DCS, process can be interconnected via a computer network to a presentation system, which consist of one or more main control computers. The presentation system can also be implemented at a later stage if financial or other reasons should require so.
If above selected strategy concerning a decentralized modular design are continued to the presentation system itself, a personal computer platform consisting of standard modules both as regards the hardware and the software will be used. Figure 1, shows the automation process may be stopped at any level.
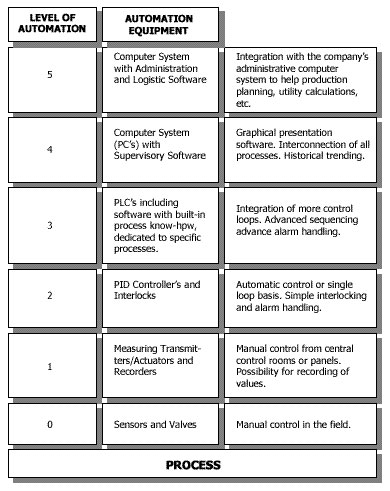
Automation for the milling plant section
The control system scheme for the milling plant section is shown in Figure No. 2 and briefly describes on the following paragraphs.
The load current of the cane leveler, cane knives and unigrator indicates of the amount of cane being fed in the mill. The level of the cane chute of the first mill controls the speed of the feed conveyors. In case the level of the cane exceeds a preset high level, then the speed of the conveyors is reduced and vice versa.
By controlling the level of the first cane chute, the mill functions properly resulting in a constant flow of material to the nest mills. In these mills, the levels of cane chute adjusts automatically as long as the general crushing rate control is active and the speed of all mills are controlled accordingly. It is not advisable to control the level of the cane chute by changing the speed of the mill, as the response time is low on account of the high inertia of the mills. Thus, the speed of the mills depends only on the set-point cane-crushing rate.
The cane carrier has a set speed ratio from one to the other to ensure uniform feed/load to all the mills.
The flow of the imbibition water is controlled to maintain raw juice of constant brix at the output of the milling plant section. The brix measurement provided before the inlet to the raw juice scale assists in automatic control of imbibition water flow as there is considerable time delay between the cane feed to the instant it reaches the last but one mill.
The automation control concept described ensures constant flow of raw juice out of the mill section as also raw juice of constant brix. This ensures efficient performance of the succeeding section namely the clarification and the evaporator sections.
Figure 3 shows the Proposed System Configuration for Milling Plant Section.
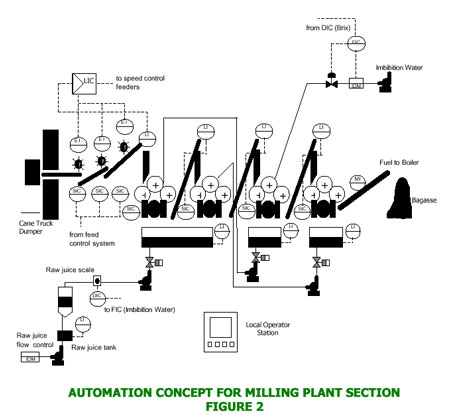
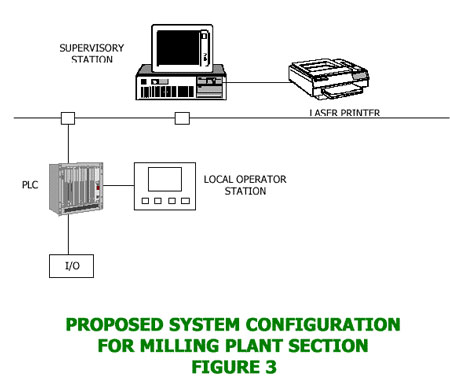
Automation concept for vacuum pan or sugar boiling process
The vacuum pan in the sugar factory constitutes a unit with well-defined borders to the surroundings and therefore especially suitable for automation. For a more efficient sugar production, the first step is to automate vacuum pans because about one third of the total energy amount is used within the sugar processing house. Therefore a quick return of investment is assured.
The main requirements to an automation control system strategy that enables efficient automation of the vacuum batch pans are:
- Proven performance and reliability in sugar applications.
- High availability
- Robust design, high degree of protection
- Low initial investment due to modular design
- Flexibility
The vacuum pan automation is design as an event controlled sequential control. Variations in the juice quality, disturbance variables in the steam and vacuum control are taken into account. The individual process steps are determined by the technology of the sugar boiling process. For every technological step there is a step in the sequential control.
Steps like seeding, graining, or boiling are difficult to handle manually and contain a wide range of improvement for better product quality and energy saving. That is if "strike hold" becomes necessary, decreasing the vapor steam set point is more efficient instead of opening the water valve. Automatically controlled and reproducible seeding and graining steps enables the crystals to grow close to the physical possible maximum speed without generation of undesired fine grain or what is called false grain.
Once the full cycle program is started, no further operation by the operator is needed. Only seeding has to be carried out manually where the automatic slurry system is available in the plant. Disturbances in the process like no juice available, mingler is full or a total vacuum breakdown is announced and the program runs same position in order to keep the strike alive.
Changing from automatic to manual operation may be carried out at any time. For pans, which are not fully equipped with remote, operated valves, a par cycle mode is available. A park cycle mode covers the most important process steps starting with "seeding" and finishing with "tightening." Both modes are possible.
General aspects of crystallization
One aim of the automated boiling process is to produce a defined number of crystals of a defined size. There are basically two methods to obtained crystals in the vacuum pan. In one method, the crystal is produced directly in the vacuum pan by seeding (shocking or seeding).
In the second method, a complete crystal (so-called footing) is put in. Using the seeding method in a second pan normally produces the footing. The completed footing is stored in a mingler or filled directly from the footing device to the vacuum pan. Both ways are possible in the concept.
Drawing in
The batch pan is set under vacuum and filled with juice up to a preset level (normally until heating chamber is covered). If existing, the agitator is started when covered. The pressure controller for heating steam is activated.
Concentration
In this step the juice is concentrated by evaporation of water until the seed point is reached. There is one seed point for seeding and one for footing. If present density is reached a light/alarm comes on to ask operator to "Prepare Seed." This is the only action the operator has to do manually during one strike.
Seeding
When seeding point is reached and the operator prepared seed, the system opens the seeding valve for a preset time. If "footing" mode is used, the systems opens the footing valve until preset level is reached.
Graining
The grain formation phase is the most critical phase of the whole sugar boiling process. The control system handles the complete section of crystal graining automatically. Both the dissolving of crystals and the generation of fine grain are avoided. Regardless of the determination of the seeding point, the system will optimize the phase of "graining" automatically. If "footing" mode is used, the graining phase is skipped.
First boiling
During the "first boiling" the sugar crystal grows to the desired size. The growing sugar crystals generate a deviation to the measuring signal of the density measurement. In order to compensate this, the set point of the density controller is adapted automatically. The set point of the density controller changes according to a curve defined by a polygon in order to reach optimized results. Using the control system, "first boiling" finishes in a minimum time while generation of fine grain is reliably avoided. For strikes that are boiled in "footing" mode there is a second polygon defined. The end of the "first boiling" is reached when a maximum level has been reached in the vacuum pan.
Brixing-up
In this step of the juice valve is closed and further extraction of sugar of the mother liquor (juice around the crystals) proceeds. The brixing up period is kept as short as possible. When the massecuite (crystals and juice) has reached a preset density or viscosity the strike is finished.
Discharging
In this section, the vacuum pan is broken (vacuum valve closed, ventilating valve and/or steaming-out valve are opened). When normal pressure has been reached, the discharge valve is open and the pan is discharge into the mingler. Discharged is completed on the level signal "0" and after a certain delay time. All this happens automatically.
Steaming out
Opening the steaming out valve cleans the pan. Finishing of "steaming out" is determined either by a preset time or maximum temperature. Steaming out is automatically handled by the system.
Pan empty
In this step, the system is reset. The control is ready for the next strike.
Following this concept and principles lead to an increase of total sugar production, a decrease of energy consumption and a decrease of boiling times. Moreover the completely automated operation of batch vacuum pans allows a reduction of personnel required in the sugar-processing house.
Figure 4 shows the automation concept for Sugar Boiling Process
Figure 5 shows the Sugar Boiling Process Proposed System Configuration.
The supervisory system consists of a graphic user interface-to DCS that allows control, supervision and data collection from the individual processes in the factory. The information is transmitted from the factory floor to the control room and the offices. Here, data can be used for follow-up on production, increasing the process efficiency and maintenance planning.
The objective of the supervisory system is to make the various production equipment from suppliers form an integrated whole, where everything runs in real time – e.g. that "real" data are collected and displayed. In this connection, all process sections are integrated including the old control and instrument systems.
Subsequently the presentation system can be integrated into the other Information System Department-system of the factory, to exchange data. For example for production planning and statistical purposes.
Based on the supervisory system the following criterions for specification of equipment can be established:
- The supervisory system software has to function on different data platforms, with windows as the primary. Be able to use the data world's open standards, in real time so, data can be exchanged with other PC program package, e.g. spreadsheets. This gives access to the very large range of existing software for PC systems.
- The software must include I/O drives for as large a selection of different control systems as possible and be able to handle several of these simultaneously. It has been tried several time to define standard protocol for data communication for automation systems. The fact is that none of these attempts have really succeeded and the market today contains a large number of different type of protocols.
- The software must be simple to configure both regarding the structure of the database and the graphic display. Likewise, the operating interface has to build up in a logical and user-friendly format and include modern presentation system such as alarm system, trend system, report generator, high-resolution graphics, etc. A number of PC's are integrated into a network, given the possibility of more works stations, which can be placed anywhere on the plant, thus achieving higher operating safety. An error on one of the operating stations only influences that specific station, while the rest can still be used.
Figure 6 shows the proposed supervisory control system concept.
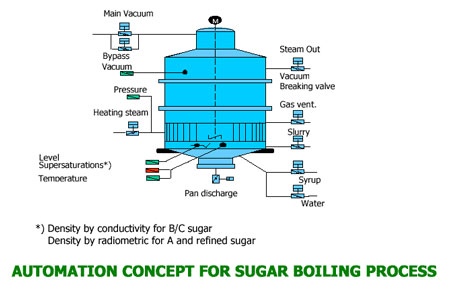
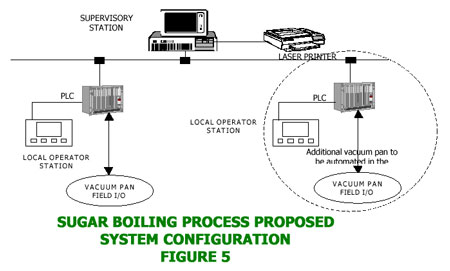
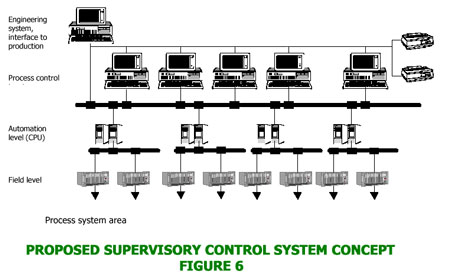
Summary and conclusions
The presented control system strategy provides a flexible and reliable system, which can be gradually extended both in size and functionality. The development of automation and control system strategies executes very fast with new and faster communication systems. A system built-up according to this principle and concepts enable the end user to choose freely among the best of the equipment available.
One can also choose equipment dedicated to special process sections produced by automation and process experts, thus utilizing the best process know-how available.
This article is provided courtesy of the ISA - the Instrumentation, Systems, and Automation Society.