Plant modernization feasibility study and justification
With the current wave of corporate takeovers and plant acquisitions, new challenge is emerging for control system engineers, consultants, and control system manufacturers.
As the new and existing plant managers strive to make these manufacturing plants safer and more productive to stay in business, a relatively small investment in upgrading the control system can result in quick return on investment (ROI).
With the currently available automation technology a 100% return on capital investment in one year is easily obtainable.
Contents
Introduction
Business objectives
Process objectives
Control system objectives
The feasibility study matrix
Life cycle cost
Life cycle return on investment
Summary
Introduction
This paper describes a methodology for conducting feasibility studies to facilitate the gathering of information and quantifying the economic, process and control system objectives by providing a clear link between the business objectives and the technical requirements to meet these objectives over the expected lifetime of the system.
The methodology of justifying control system upgrades starts by defining the following objectives:
- Business objectives
- Process objectives
- Control system (or automation system) objectives
The next step is to estimate the following items:
- The initial investment in the new system
- Additional life cycle costs
- The life cycle Return On Investment (ROI)
The plant to be modernized is then partitioned into process areas as shown in the example in Figure #1
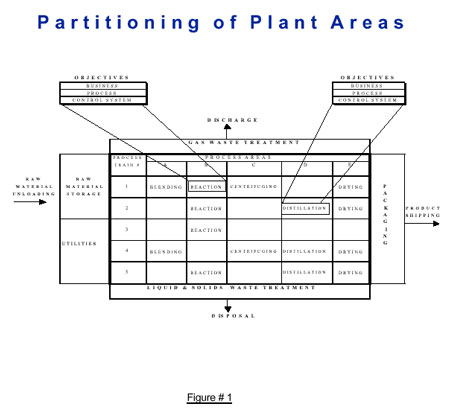
The areas that are most likely to be targeted for modernization are identified; they are usually bottlenecks in meeting the required throughput or product quality.
In this example the reaction area in the first process train #1 and the distillation area in process train # 2 are identified as potential targets for modernization.
The business, process and control system objectives of modernizing each process area is then evaluated.
The return on investment is usually small for the first area to be modernized due to the high initial investment in the new equipment and the learning curve involved in training the plant operators.
However the real rewards start to show as additional process areas are upgraded using the same automation system (see figure # 2).
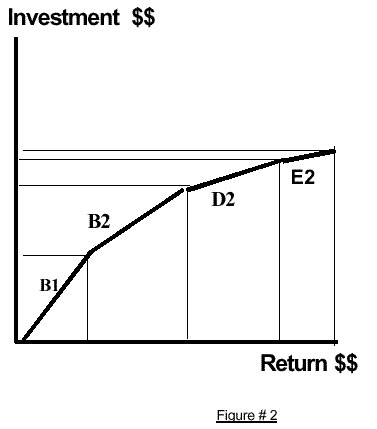
Return to Table of Contents
Business objectives:
The following is a list of typical business objectives that can be identified as benefits and quantified:
- 1. Increase sales:
- If the existing product is sold out, by decreasing the cycle time the throughput can be increased and that will increase the sales volume.
- By adding new products using the same process equipment and modernized automation system, additional sales revenue can be realized.
- If the quality of the existing products can be improved, a higher price can be charged which will increase the profit margin.
- a. Existing products:
b. New products:
2. Improve product quality:
3. Decrease manufacturing cost:
- One of the most common and often misunderstood benefit of automation is decreasing manpower, as a way to decrease manufacturing cost, however there are other tangible benefits that are often overlooked.
The way to identify these benefits is by looking into the process objectives, for example savings in the use of raw material and utilities.
Return to Table of Contents
Process objectives:
This is an intermediate and very important objective that must be evaluated before we go to control system objectives.
The process objectives translate the benefits from the business objectives to a high technical level of detail involving the existing plant design, operating procedures, and the physical and chemical characteristics of the product itself.
The following is an example of typical process objectives:
- Increase throughput
- Add new products
- Decrease wasted batches
- Improve quality
- Decrease raw material usage
- Energy and utility savings
- Decrease disposal cost and environmental compliance penalty
- Increase equipment life
- Increase labor efficiency
Return to Table of Contents
Control system objectives:
This is the most technically detailed objective in the feasibility study, and from this step an accurate estimate of the investment of the installed automation system hardware and software can be established.
The following is an example of some of the Control system objectives:
- Increase system capacity:
- Add monitoring points
- Add control loops
- Add I/O's
- Add operator consoles
- Add monitoring points
- Increase system capabilities:
- Automate batch sequence
- Add on-line analyzers
- Automate recipe management
- Automate batch reporting
- Automate batch sequence
- Increase system availability and reliability:
- Use fault tolerant shutdown system
- Add redundancy
- Use transmitters instead of process switches
- Use fault tolerant shutdown system
- Optimize process:
- Use expert system (knowledge based)
- Add SPC & SQC
- Develop simulation model
- Use advanced controls
- Automate production unit scheduling
- Use expert system (knowledge based)
Return to Table of Contents
The feasibility study matrix:
A feasibility study matrix can be filled-in showing the benefits and the cost t reach all the business, process and control system objectives.
In one example, the importance of each control system item to meet the objectives is given a rating (M = Must, W= Want)
The total installed cost of the new system can be estimated using this Feasibility Matrix.
Return to Table of Contents
Life cycle cost:
The life expectancy of the system can be established based on the useful life of the plant equipment, the current technology trends, usually a lifetime of 10 to 14 years is realistic.
The life cycle cost can then me calculated by adding:
- Estimate the installed cost of the new system
- Estimate Additional Annual Engineering cost
- Estimate Additional Maintenance costs
Return to Table of Contents
Life cycle return on investment:
The life cycle ROI is simply = Life cycle Benefits – Life cycle costs
Most operating companies consider a return on investment in automation of less than one year is quite acceptable, and for a more long range prospective, the life cycle ROI provides an even greater incentive to invest in plant modernization using automation.
Return to Table of Contents
Summary:
In order to have a credible justification of a plant modernization project using the automation technology as the tool to realize this goal, a clear methodology is needed to link the business needs of the enterprise to the automation tools required to meet these needs.
The following six steps were used in this paper as basis for this methodology:
- 1) Define the business and process objectives
2) Estimate the life cycle benefits the modernization project.
3) Perform the technical feasibility study for automating potential plant areas ("Musts" and "Wants")
4) Estimate the initial investment and the life cycle costs of the upgrade.
5) Estimate the life cycle ROI
6) Monitor the life cycle ROI to keep the business and the control system objectives on the same track over the long term.
Return to Table of Contents
About the author
Alex Habib is a Principal Automation Engineer working for Walsh Automation, MSEE, 15 + years of hands-on experience in automating and modernizing pharmaceutical, food, and specialty chemicals plants and research facilities.
Alex Worked at: Merck, Rhone-Poulenc, Olin Chemicals, Jacobs Engineering, and Hoffmann La Roche.
This article is provided courtesy of the ISA - the Instrumentation, Systems, and Automation Society.