Emerson Applies Oxymitter In-Situ Sensors To Improve Catalyst Regeneration Efficiency At Total In Belgium
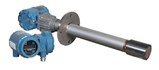
Austin, TX - Rosemount® Analytical Oxymitters from Emerson Process Management have replaced the previous sample extraction-based oxygen measurement system used on the catalyst regeneration unit at Total Raffinaderij Antwerpen, Belgium. The more reliable readings from the Oxymitter are believed to have improved continuous catalyst regenerator (CCR) performance, helped the plant increase safety, and reduced the maintenance time and effort that needs to be allocated for critical catalytic reformer refinery operations.
The Total refinery in Antwerp is believed to be the second largest refinery in Europe, at 360,000 bpd, fed by pipeline from supertankers unloading at Rotterdam. Catalytic reformers are used to improve the octane rating of the gasoline fractions produced. Carbon is deposited on the catalyst during this process, so a portion of the catalyst is continuously extracted and routed to the CCR where the carbon is removed by burning it away in an oxidizing atmosphere.
Measurement of oxygen in the regenerator is believed to be key to controlling the safety and rate of burn-off of this carbon and maintaining regeneration efficiency. Further, expensive platinum catalyst can become fused if the oxygen levels and bed temperatures are not maintained within set limits. The Rosemount Analytical Oxymitter, being an in-situ probe, where the sensor at the end of the probe is placed into the process, avoids the problems that were inherent with previous extractive analyzer systems, where the sample lines tended to become plugged with catalyst fines and hydrochloric acid condensation. Installations using the Oxymitter avoid the costs and downtime caused by such plugging, and operators can run their regenerator control system continuously, with fewer maintenance interruptions. A reliable measurement of oxygen level gives the operator the confidence needed to run the CCR unit at the optimum rate of regeneration. The Oxymitter has been in service for seven months and has performed with accuracy and reliability. This excellent product performance was expected since many other Oxymitter units have been installed around the plant on flue gas analysis systems. In this application, the pressurization option on the Oxymitter is used to compensate for the 2 bar operating pressure in the regenerator. The response and assistance provided by Emerson during installation was much appreciated. With the HART diagnostic functionality, the instrument engineers within the Total refinery can use the predictive maintenance information provided, and can thereby increase overall reliability. A second Oxymitter unit will be installed soon.
The advanced Emerson technology in the Rosemount Analytical Oxymitter, a zirconia based oxygen sensor, is believed to be recognized worldwide, and has become the standard for efficient monitoring of oxygen levels in catalyst regenerators on many petrochemical plants, including fluidized catalytic cracking unit (FCCU) regenerators.
SOURCE: Emerson Process Management