Davron Manufactures Continuous Scorch Machine In U-Shape Arrangement
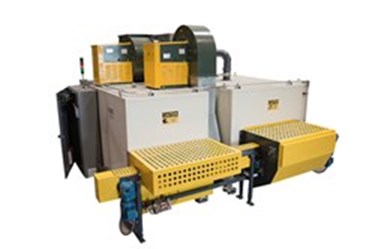
Davron Technologies, Inc. designed and manufactured the DTI-1134, an electric continuous scorch machine that is used in the manufacturing of disc brake pads for the automotive industry.
Chattanooga, Tenn. (PRWEB) - Davron Technologies, Inc. designed and manufactured the DTI-1134, an electric continuous scorch machine that is used in the manufacturing of disc brake pads for the automotive industry. The system features both a scorch chamber and a cooling chamber. Most scorch systems have scorching and cooling in-line. However, to save plant space, the DTI-1134 positions the scorch chamber and cooling chamber in a U-shape arrangement. With a two-minute scorch cycle and two-minute cooling cycle, the DTI-1134 continuous scorch machine processes 1,900 disc brake pads per hour.
The DTI-1134’s scorch chamber utilizes two heated platens, each platen featuring 21 electric rod heaters for a total of 42 heaters. Featuring four independent zones of temperature control, the platens can be programmed to operate between 212ᴼ and 1,328ᴼF. The conveying system in the scorch chamber consists of custom pusher bars that move the disc brake pads across the heated platens. A variable frequency drive (VFD) was included as part of the conveying system to allow for adjustability in scorch time.
The DTI-1134 continuous scorch machine also includes a transfer conveyor to move pads from the scorch chamber to the cooling chamber. The cooling chamber uses a flat wire conveyor belt with VFD control. Cooling is achieved by impinging air on the bottom of the pads from below the conveyor belt. Parts are cooled to approximately 122ᴼF in two minutes. All functions are controlled by PLC with operator touch screen (HMI) and the control panel meets UL508A guidelines and includes a UL508A label.
The overall dimensions of the DTI-1134 continuous scorch machine are 12’5” wide x 6’7” high x 12’7” long. The scorch chamber’s usable interior dimensions are 5’4” wide x 6’8” long. The inner chamber is made out of 16-gauge aluminized steel backed by six inches of eight-pound density mineral wool insulation. The exterior is constructed from 16-gauge carbon steel and is backed by a structural steel frame and finished with high-temperature paint. Usable interior dimensions of the cooling chamber are 3’6” wide x 9’10” long. A structural steel frame supports the cooling chamber. The interior is made out of 16-gauge aluminized steel with the exterior constructed from 16-gauge carbon steel. It is finished with high-temperature paint.
Davron designed the DTI-1134 based on three criteria provided by the customer: the scorch temperature, total cycle time, and available space in the plant. Per Davron’s suggestion, the system was engineered in the U-shape arrangement and the electrical enclosure was designed to minimize floor space. Once acceptance and training were completed at Davron headquarters, the customer took possession of the DTI-1134 and installed the system at their facility.
Visit http://www.davrontech.com for more information about Davron’s continuous scorch machines or continuous conveyor oven capabilities. Or, if you’d like to discuss your own industrial oven project, please call Davron’s Vice President, Jimmy Evans, at (888) 263-2673, or fill out Davron’s online spec submission form.
About Davron Technologies, Inc.
Davron Technologies, Inc. custom fabricates industrial ovens, providing turnkey design and system integration services to develop thermal processing solutions. Davron is a total industrial oven manufacturer, creating custom industrial ovens and precision process equipment for every industry that requires thermal processing. Each Davron industrial oven is custom built according to customers’ unique specifications. As the Provider of Industrial Oven Solutions, Davron offers one of the largest selections of in-house and on-site industrial oven services in the world.
Source: PRWeb
View original release here: http://www.prweb.com/releases/2014/02/prweb11545602.htm